Summarize the cause of the collision, know these reasons, will avoid the knife accident in the machining center, reduce unnecessary losses. CNC machining center will inevitably have a knife if it is mishandled, etc. If there is a collision, how to diagnose it The reason for the collision knife, what are the reasons for the common collision knife? The following summarizes the causes of the collision knife. Knowing these reasons, it will avoid the knife accident in the machining center and reduce unnecessary losses.
First, the problem of the machine origin and coordinate system will cause the knife
First of all, we should think of the setting of the origin of the machine coordinate system. This machine tool* in the incremental configuration is obvious. When the machine is turned on, the machine origin is not set. At this time, the program is run, and the machine will be hit by the knife because the system I don't know the exact position of the machine, and the machine origin is not correct. For machine tools that use the incremental position encoder, the zero return position is not correct and the position of each zero return is incorrect. Therefore, it is necessary to adjust the loading position. If the machine origin setting is incorrect, the knife is prone to occur when running the program.
Next is the setting of the workpiece coordinate system. Before the machining operation, the zero point setting of the workpiece coordinate system (G54-G59) is incorrect or the coordinate system is incorrect. At this time, the machining is likely to cause the collision or the size of the workpiece to be processed incorrectly.
Second, the parameter setting is wrong or incorrectly changed. The data unit is confusing during processing, and the workpiece is prone to incorrect size or caused by a knife.
(1) Everyone knows that the machine tool is in accordance with the procedure. If there is a problem with the given program itself, it will definitely hit the knife. Some of the G codes of FANUC are modal. If the G code of the previous machining program or block in the program is not canceled at the end of the block, it will continue to be valid in the next program or block, which may cause the machine to malfunction. Or cause a knife.
(2) The setting parameters are incorrect or incorrectly changed.
NO 000#2 INI setting error 0: Metric unit 1: Imperial unit.
NO 3401#0 DPI uses the address word of the decimal point, the meaning of the decimal point. When the decimal point is omitted,
0: Set * small setting unit
1: Consider the mm inch angle as 1°.
Third, the wrong operation in the process
(1) During the normal processing of the program, the program is stopped due to misoperation. If the operator accidentally presses the "RESET" to reset the cycle immediately, the collision is likely to occur.
Cause: The default value of the operation and the set value of the program change. Press: RESET: Reset resets the CNC system to the initial state, clears the prediction program information stored in the DRAM, and may also change the movement command of the tool.
G90 Absolute command: Run according to the coordinate value of the command.
G91 Incremental value command, executed according to the moving distance of the command.
Avoidance method: If the program stops running when the error occurs during the automatic running of the program, change it to edit mode at this time, press RESET to reset the program, and re-run the program. Even if you convert from MDI to MEM, be sure to check each modal code. (GMSFT, etc.) After the disease is confirmed to be correct, the automatic cycle is started, otherwise serious consequences may result.
(2) There is also a knife compensation value setting error.
If the tool compensation value is set incorrectly, it will also cause a knife strike. Regularly check that the tool compensation value is correct to avoid a knife accident.
In fact, CNC machining centers cause many collisions, but the possibility of failure caused by system hardware is very small. As long as the management is strengthened, the misoperation is reduced, the setting of the tool compensation value and the workpiece coordinate system is checked regularly, the origin is confirmed before processing, and all aspects are checked. Most of the collision accidents can be avoided.
CNI as a world`s leading designer and manufacturer of Laser system, fully understood your actual demands of Laser Measurement and analytical capability, designed several laser safety protection instruments which are specially tailored to you. Based on the understanding of practical applications, advanced technology and precise selection of devices, CNI dedicated to helping you find the best choice which can not only meet your measurement requirements, but also offer the most competitive price. The modular options we offered made it easier for you to extend the configuration when your demands increased or changed in the future, which improved the cost performance.
In addition, we also provide data testing and customized services of laser safety protection system, which are based on customer`s needs.
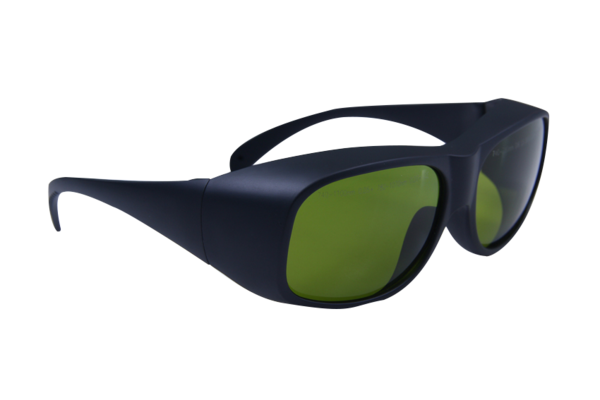
Laser safety is the key important thing during laser operation. CNI can offer proper laser goggles that protect from laser damage. There are different kinds of laser goggles for different wavelength.
Laser goggles with beautiful shape, comfortable fit, high definition, extrusion deformation prevention material, are able to protect human eyes from the laser radiation damage from 200-11000nm.
Laser Safety,Laser Eye Safe,Laser Safety Glasses,Safety With Laser
Changchun New Industries Optoelectronics Technology Co., Ltd. , https://www.opticsqm.com