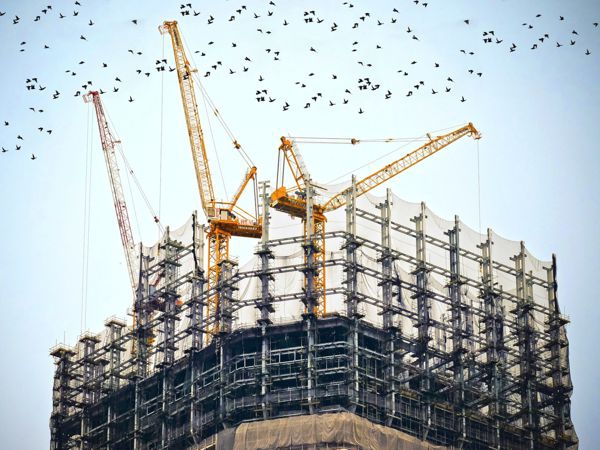
Cranes Are Often The Most Powerful Equipment On The Job
Cranes are typically the largest and most powerful machines on construction sites. Their incredible strength allows them to lift and move extremely heavy loads, but this same power also makes them potentially dangerous if not handled properly. These complex machines require strict adherence to safety protocols to protect workers and bystanders alike.
According to research from OSHA and the Bureau of Labor Statistics (BLS), around 40 construction workers lose their lives each year due to crane-related accidents. To mitigate these risks, cranes weighing more than 2,000 pounds must be operated by certified professionals through the National Commission for the Certification of Crane Operators (NCCCO). Companies that operate cranes are legally responsible for any harm or damage caused, which is why many invest in specialized insurance coverage.
Crane Safety Toolbox Talk
Checklist of critical items to monitor before moving a load
- Inspect the area for overhead hazards like power lines, trees, and structures.
- Confirm that all slings, chains, and straps are rated for the load’s weight and have proper tags indicating their safe working load.
- Identify and mark pinch and crush zones around the crane and the load area with paint or chalk for visibility.
- Set up barriers around the crane's swing radius to prevent unauthorized access to hazardous areas.
- Ensure the load is balanced and free of obstructions along its path.
- Develop and distribute a detailed lift plan to all involved personnel. Any changes should be communicated clearly to everyone on site.
Checklist of critical items to monitor while moving a load
- No one should be under or near a suspended load during operation.
- Keep all personnel at a safe distance from the crane during lifting operations.
- Operators must remain focused and avoid distractions like phone calls or texting.
- A trained signal person is required, and both the operator and signal person must use standardized hand signals. They must maintain clear communication and visual contact at all times.
- Only one person should give signals at a time unless multiple signals are needed for safety reasons.
- Use an air horn to alert nearby workers when a lift is in progress. This helps ensure awareness even for those not directly watching the crane.
- Avoid raising the load higher than necessary to reduce risk.
- Never leave a load hanging in the air unattended.
Toolbox Talk Outline
- Start with a discussion of the day's task.
- Go over the safety checklists provided.
- Review potential hazards, environmental conditions, PPE requirements, first aid procedures, and emergency responses.
- Allow time for questions and feedback from the crew.
- Conduct a quick quiz to ensure understanding of the safety guidelines.
Safety Equipment - Signs, Stickers, Air Horns & Lights
Safety Signs and Stickers
Visual signs and stickers are essential tools for communicating risks on a job site. OSHA and ANSI provide standards for safety signs used with cranes. These signs help raise awareness among workers and visitors about potential dangers.
Crane warning labels are often made from durable materials such as vinyl, polyester, or aluminum. You can find a variety of options on websites like SafetySign.com and Amazon. In multilingual areas, consider using bilingual signs to ensure clarity for all workers.
Sample Safety Signs
Source: SafetySign.com Note: Equipment Radar is not affiliated with or sponsored by SafetySign.com.
Air Horns and Audible Alarms
Before starting a lift, use an air horn or audible alarm to notify everyone nearby. After the lift is complete, use an "all clear" signal to inform people that it's safe to return to the area. Different horn patterns can be used to indicate the start, middle, and end of a lift.
Audible cues are especially important because not everyone may be within direct line of sight of the crane. Using an air horn ensures that all workers are aware of what's happening above them.
Safety Lights
Proper lighting is crucial for crane operations, especially in low-light conditions or during inclement weather. Lights help distinguish the crane from its surroundings and improve visibility for operators and workers.
Warning lights can be placed around the crane to draw attention to its presence and the associated risks. This is particularly important in busy or high-traffic areas.
Transportation
Moving a crane to a job site requires careful planning, especially in urban or industrial environments. Study the route in advance and measure all dimensions to ensure the crane can pass safely. Include extra space for turns and tight spots.
It's common to use spotters to guide the crane through tight spaces. Maintain constant communication between the driver and spotters to avoid accidents.
If the crane is oversized, follow local laws and regulations. This may include adding flags, bright signs, or even police escorts. Also, check weight limits for bridges and elevated roads to avoid structural damage.
Lift Plan
A lift plan is similar to a blueprint — it outlines how the job will be done step by step. It's usually created by a qualified engineer and includes details such as:
- Load weight and crane capacity
- Center of gravity location
- Dimensions of the load
- Lifting points and rigging equipment
- Height restrictions and obstacles
- Risk assessment and mitigation strategies
- Method statement with procedural details
Distribute the lift plan to all relevant personnel and update it whenever changes occur. Keeping everyone informed is key to a successful and safe operation.
OSHA Crane Safety Hand Signals
Crane operators and signal persons must use standardized hand signals to communicate effectively. OSHA has developed specific guidelines for these signals, which are widely used across the industry.
Arm extended horizontally, palm down, swung back and forth.
Both arms extended horizontally, palms down, moved back and forth.
Arm extended to the side, forearm and index finger up, small circles.
Arm extended horizontally, thumb up, fingers closed.
Arm extended horizontally, index finger points in direction of swing.
Hands at waist level, thumbs pointing at each other, fingers closed.
Arm extended horizontally, thumb up, fingers open and close while load moves.
Hands together at waist level.
Arm and index finger pointing down, small circles.
Arm extended horizontally, thumb down, fingers closed.
Hands at waist level, thumbs pointing outward, fingers closed.
Fingers up, arm extended forward and backward in direction of travel.
Arm extended horizontally, thumb down, fingers open and close while load moves.
Hand placed in front of the action signal.
Arm bent at elbow, forearm vertical, tapped with other hand. Then regular signal indicates action.
Rotate fists around body; rotation away from body = forward; towards body = backward.
Hand taps top of head, then regular signal is given.
Raise fist on the side to lock track. Rotate other fist in direction of travel.
Palm up, fingers closed, thumb points in direction of motion, hand jerked horizontally.
Source: Full OSHA Crane Guidelines
Crane Rental
Many crane rental companies offer more than just equipment. They often provide safety resources, certified operators, transportation services, and even assistance in developing lift plans. Since every job is unique, it's always a good idea to consult with your rental company to ensure you get the right support and guidance.
Resources
12 types of cranes
OSHA Crane, Derrick and Hoist Safety
Crane safety video
Find Similar Articles By Topic
#cranes #material handling #checklists #construction #toolbox talks
An inclined bed CNC machine offers several advantages over a flat bed CNC machine. Here are the key advantages:
-
Enhanced Rigidity: The inclined bed design provides better structural rigidity. The inclined angle increases the machine's natural stability, reducing vibrations during machining operations. This enhanced rigidity improves machining precision, accuracy, and surface finish quality.
-
Improved Chip Evacuation: With an inclined bed, chips and coolant can flow naturally away from the workpiece, aiding in efficient chip evacuation. This reduces the risk of chip recutting, minimizes tool wear, and improves overall machining performance.
-
Accessibility and Visibility: The inclined bed design allows operators to have better access to the workpiece and improved visibility of the machining process. This makes it easier to set up, monitor, and adjust machining operations, enhancing productivity and reducing errors.
-
Compact Footprint: Inclined bed CNC machines typically have a smaller footprint compared to flat bed machines. This saves valuable floor space in the workshop, allowing for better layout optimization and efficient use of available area.
-
Ergonomics and Operator Comfort: The inclined bed design reduces the need for operators to bend or reach over the machine, promoting better ergonomics and reducing the risk of strain or injury. It offers improved operator comfort and ease of operation.
-
Chip Management: The inclined bed design facilitates efficient chip management. Chips can be easily collected and removed, reducing the risk of chip buildup, minimizing maintenance requirements, and prolonging tool life.
-
Tool Life and Performance: The enhanced rigidity and stability of an inclined bed CNC machine result in reduced tool deflection and improved cutting performance. This leads to increased tool life, better machining efficiency, and cost savings in terms of tool replacement and downtime.
-
Versatility: Inclined bed CNC machines are versatile and can handle various machining operations, including turning, milling, drilling, and tapping. They can effectively machine a wide range of materials, from metals to plastics, allowing for diverse applications in different industries.
Inclined Bed Cnc Machine,High Rigid Inclined Cnc Bed Machine Tools,Inclined Body Bed Cnc Lathe,Inclined Flat Bed Cnc Machine
Ningbo Leyan Machinery Technology Co., Ltd , https://www.cncleyan.com