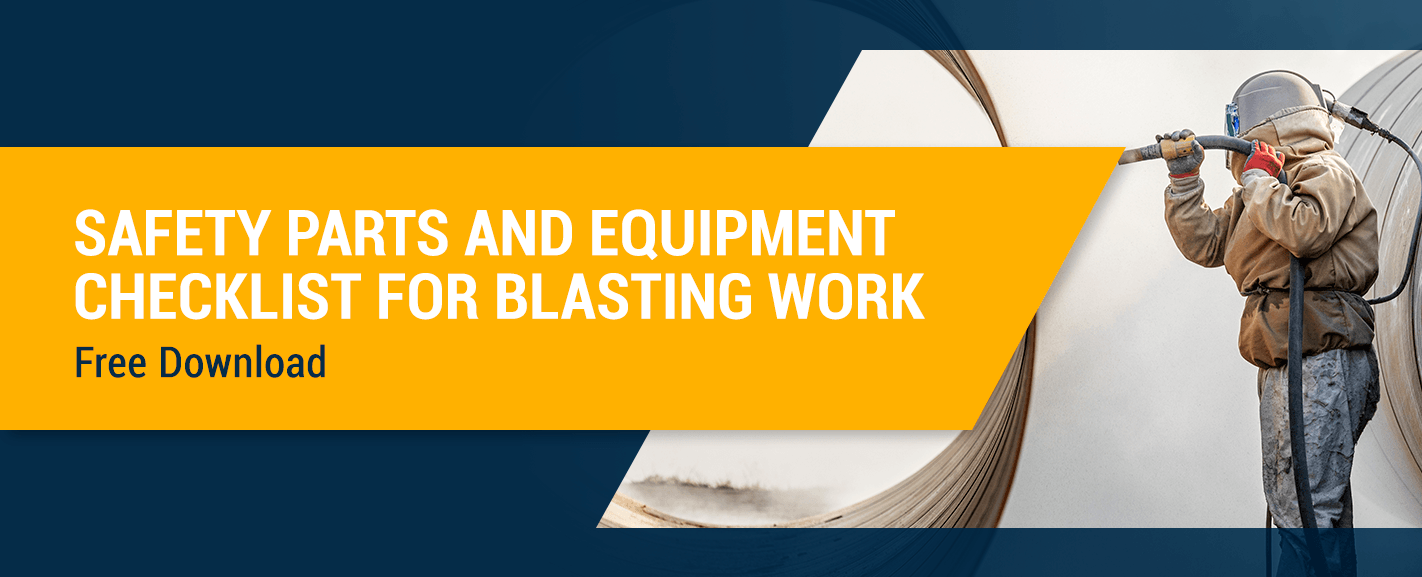
Abrasive Blasting Checklist
Updated: March 20, 2023Abrasive blasting is a widely used process across many industries, from shipbuilding to automotive manufacturing. It allows for efficient surface preparation, making it ideal for painting, sealing, or applying texture. However, because of the high pressure and force involved, safety must always be a top priority.
Employers must ensure that workers are properly equipped with protective gear. Safety equipment should not only be effective but also comfortable to allow for maximum productivity. When employees feel safe and supported, they can focus better on their tasks and work more efficiently.
In addition to PPE, regular maintenance and inspection of abrasive blasting equipment are essential. This helps prevent malfunctions and ensures that all tools are in good working condition before use. Proper training and adherence to safety protocols are equally important to reduce the risk of accidents.
This guide outlines the most common hazards associated with abrasive blasting and provides a comprehensive checklist for safety equipment and procedures. Whether you're a seasoned professional or new to the field, following these guidelines will help keep your team safe and your operations running smoothly.
Contact Us
What Is Abrasive Blasting?
Abrasive blasting, often referred to as sandblasting, is a method that uses compressed air or water to propel a high-speed stream of abrasive materials at a surface. Its primary purpose is to clean, remove rust, prepare surfaces for coatings, or add texture. This technique is fast and effective, making it a popular choice in many industrial applications.
What Materials Are Used for Abrasive Blasting?
The type of material used depends on the job requirements and the surface being treated. Common abrasives include glass beads, crushed glass, aluminum oxide, plastic, silicon carbide, steel shot, steel grit, Starblast™, Black Beauty®, ground walnut shells, and ground corn cobs. Each has unique properties that make them suitable for different applications.
- Glass beads: Eco-friendly and free of silica, ideal for light cleaning without damaging the substrate.
- Crushed glass: Aggressive cutting action, great for heavy coatings.
- Aluminum oxide: Versatile and durable, used for rust removal and etching.
- Plastic: Lightweight and less aggressive, suitable for soft surfaces.
- Silicon carbide: Hard and fast-cutting, reusable to save costs.
- Steel shot: Strong and durable, used for heavy-duty jobs like removing corrosion.
- Steel grit: Angular shape for deep anchor patterns, ideal for structural applications.
- Starblastâ„¢: Uniform blasting pattern, low silica content, and reusable.
- Black Beauty®: Chemically inert, available in various grain sizes, and safe for sensitive substrates.
- Ground walnut shells: Biodegradable and gentle, perfect for delicate surfaces.
- Ground corn cobs: Soft and non-abrasive, used for polishing and cleaning.
What Are Some Hazards of Abrasive Blasting?
While abrasive blasting is efficient, it comes with several risks. The main concern is exposure to airborne particles, which can be toxic if inhaled. Other hazards include loud noise levels, high-pressure streams, static electricity, vibrations, slips, and heat. These dangers highlight the importance of proper safety measures and equipment.
- Air contaminants: Particles like silica sand can cause serious respiratory issues.
- Loud noise: Can lead to hearing loss without proper protection.
- High-speed particles: Risk of injury from flying debris.
- High-pressure streams: Can cause severe injuries if not handled carefully.
- Static electricity: Improper grounding may result in electric shocks.
- Vibration: Prolonged use can lead to hand-arm vibration syndrome.
- Slips and falls: Wet or uneven surfaces increase the risk of accidents.
- Heat exposure: PPE can contribute to heat-related illnesses in hot environments.
Safety Equipment Checklist
To minimize risks, it's essential to use the right personal protective equipment (PPE). At Finishing Systems, we offer reliable and comfortable safety gear designed for abrasive blasting. Here’s what you should include in your safety checklist:
- Respirator: Protects against harmful airborne particles. We offer air-supplied models with built-in hearing protection.
- Climate control device: Helps manage temperature inside the respirator for comfort in extreme conditions.
- Eye and face protection: Essential for protecting against flying debris.
- Gloves: Durable, vibration-resistant gloves that protect the entire forearm.
- Apron or blast suit: Provides full-body protection from abrasive particles.
- Safety shoes: Non-slip, reinforced footwear to protect feet from falling objects and sharp materials.
- Hearing protection: Ear muffs or earplugs are necessary if not included in the respirator.
How to Begin Every Project Safely
Before starting any abrasive blasting project, follow a strict safety procedure. This includes inspecting the equipment, surroundings, and PPE. Below is a detailed checklist to help ensure everything is in order:
Blasting Equipment
Your blasting system typically includes an air compressor, hose, blaster, and nozzle. Before use, check the following components:
Air Compressor
- Is the compressor maintained and serviced regularly?
- Does it have a pressure relief valve?
- Is it located upwind of the blasting area?
- Is it at a safe distance from the blasting site?
Blast Vessel
- Is the vessel free of cracks, dents, or corrosion?
- Is there moisture or debris inside?
- Are there any leaks?
- Was it depressurized before loading abrasive?
Valves, Hoses, and Fittings
- Are all parts in good condition, with no damage or leaks?
- Are there soft spots in the hoses?
- Are gaskets intact and free of wear?
- Are whip checks and safety pins installed?
- Is the blast hose at least three times the size of the nozzle orifice?
Blast Nozzle
- Is the nozzle thread or jacket damaged?
- Is it sized correctly for the job?
- Has the orifice increased by 1/16 inch? If so, replace it.
Abrasive Materials
- Is the abrasive compatible with the equipment?
- Is it free of debris?
- Have you reviewed the Material Safety Data Sheet (MSDS)?
- Is it non-toxic or within OSHA’s acceptable limits?
- Is it dry?
Objects
- Is the object securely fastened?
- Is it only used for non-flammable materials?
Environment
- Have you established a hazardous zone?
- Are electrical lines protected?
- Is the site free of tripping hazards?
- Is the area well-lit and ventilated?
- Is the blast machine on level ground?
- Are static discharge measures in place?
- Is the atmosphere free of flammable fumes?
- Is the carbon monoxide monitor calibrated?
PPE
- Does the respirator meet NIOSH standards?
- Does it cover the head, neck, and shoulders?
- Do the air filters meet OSHA Grade D requirements?
- Is the respirator undamaged?
- Are eye protection items in good condition?
- Are gloves and boots free of tears or punctures?
- Is ear protection available?
Practicing Personal Hygiene Habits During Projects
Maintaining good hygiene is crucial during and between projects. Follow these guidelines to protect your workers:
- Prohibit eating, drinking, or smoking in blasting areas.
- Provide wash stations for frequent hand and face cleaning.
- Encourage workers to remove contaminated clothing before eating or smoking.
- Offer showers and change areas at the end of shifts.
- Keep contaminated PPE out of clean zones.
Contact Finishing Systems for Your Abrasive Blasting Needs
Abrasive blasting is a powerful and efficient way to prepare surfaces for coating or finishing. With the right PPE and regular equipment inspections, you can maintain a safe and productive work environment. Prioritizing safety ensures that your team stays healthy and your business runs smoothly.
At Finishing Systems, we provide high-quality abrasives, blasting equipment, and expert support to help you complete your projects safely and efficiently. Contact us today to learn more about our products and services.
Â
Download the Checklist
NINGBO RUICAN is a professional manufacturer of Auto Parts, such as Wheel Hub,Wheel Hub Assembly,Brand Car Wheel Hub,Car Wheel Bearings,Truck Wheel Bearings, we offer different kinds of Wheel Hub,Wheel Hub Assembly,Brand Car Wheel Hub etc.
Wheel Hub,Wheel Hub Assembly,Brand Car Wheel Hub,Car Wheel Bearings,Truck Wheel Bearings
NINGBO CITY YINZHOU RUICAN MACHINERY CO.,LTD , https://www.china-sandcasting.com