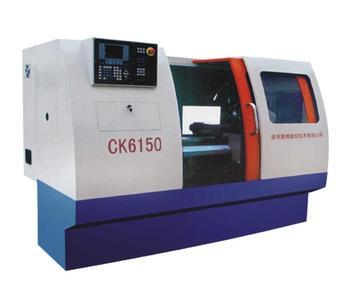
Three-phase development creates global CNC machine tool industry
The development of the global CNC machine tool industry can be roughly divided into three stages: starting, industrial application and in-depth promotion. The starting stage of CNC machine tools began in the 1950s. In 1952, in order to meet the needs of the military, the Massachusetts Institute of Technology developed the world's first CNC machine tool. Since then, Japan, Germany, and the United Kingdom have successively started research and development. However, due to limitations in electronics and computer technology, the numerical control system at that time was bulky and expensive, and the entire industry developed slowly until the late 1970s.
In the 1980s, with the wide application of integrated circuits and computer technology, CNC machine tools had a new breakthrough, and the entire industry also entered a new phase of industrial application. In addition to the increased speed and reliability of the numerical control system, the variety of machine tools and peripheral equipment has increased, and the variety of machine tools has also rapidly increased. In the 21st century, the CNC machine tool industry has entered the stage of in-depth promotion. This stage is marked by the integrated integration of CAD/CAM and numerical control systems. Moreover, after 2010, with the deep integration of intelligent control technology and networked technology, the global CNC machine tools The industry presents a new trend of development.
Industrial development presents technological diversity and regional agglomeration
CNC machine tools have become the commanding heights for the competitive advantage of the equipment industry. Since the 1960s, the developed countries have invested heavily in R&D, and the technical level has been ahead of the rest of the world. At present, the numerical control rate of the machine tool industry in industrial countries is at least 50%, and Japan and Germany are more than 70%. In high-end manufacturing technology-intensive industries such as aerospace, automobiles, and machine tool manufacturing, it is more than 80%. Due to the high degree of specialization of the CNC machine tool industry, high degree of technical integration, and wide variety of products, even in developed countries, it is impossible for a country's machine tool industry to supply all CNC machine tool parts. Therefore, some workers in the industry are highly detailed and highly internationalized. Due to the high technical content of key functional components such as numerical control systems and feed systems, the competition among countries in technology has become increasingly fierce. Moreover, with the rapid development of electronic technology, the development cycle has accelerated, the technology of CNC machine tools continues to innovate, and new products have come out one after another.
Since CNC machine tools involve many disciplines such as mechanics, electronics, and materials, the technology is highly integrated. At present, the international CNC machine tool market is monopolized by a few large-scale groups and shows a trend of high concentration in both Europe and East Asia.
High speed, precision, integration, and green become the development direction of CNC machine tools
High speed has always been the goal of CNC machine tools. Since 1990, European and American countries have applied new kinematics theories and advanced drive technologies to optimize the structure of the machine tool, improve the performance of functional components, reduce the weight of moving parts, and reduce friction in motion. The application of high-speed machining technology shortens the cutting time and auxiliary time, and achieves high quality and high efficiency in processing and manufacturing.
Precision has become an important performance parameter of CNC machine tools. By optimizing the structure of the machine tool, the accuracy of manufacturing and assembly is improved, and the reaction time of the numerical control and servo system is reduced.
Using technology such as temperature and vibration error compensation, the geometric accuracy and movement accuracy of CNC machine tools have been improved. At present, the processing accuracy of ordinary CNC machine tools can reach 5 to 10 microns, precision machining centers can reach 1 to 1.5 microns, and the precision of ultra-precision machining centers can reach nanometer level.
Integration is also one of the most important trends in the development of CNC machine tools. After 2010, CNC machine tools are closely integrated with intelligent and network technologies, and can be remotely controlled and diagnosed via the Internet, laying the foundation for the integration of CNC machine tools into the Internet of Things era.
Greening has become a new direction for the design, manufacture and use of CNC machine tools. Countries gradually incorporate greening into their research and development areas. For example, during the design process, renewable materials are used extensively. In the work process, variable frequency technology is used to reduce idle speed and energy consumption, and the use of CNC machine tools reduces waste emissions by more than 50%.
High speed, precision, integration and green have become the technological development direction of CNC machine tools. In terms of equipment level, processing scope, processing quality and production efficiency, the global CNC machine tool industry has achieved revolutionary progress and has played a key role in improving the level of high-end manufacturing.
Diesel Water Pump is powered by Diesel Engine , its advantage is advanced and reasonable structure, high efficiency, low vibration, low noise, smooth operation, reliable and easy to install and so on
According to the different functions , diesel water pump have following functions
1) Industry - boiler feed water system and cooling cycle system
2) Smelting - water supply circulating system and cooling system
3) Fire hydrant system, sprinkler system, spray cooling system, foam system, water gun system
5) Military - field water supply system, island fresh water collection system
6) Municipal - emergency drainage, emergency water supply
7) Agricultural - irrigation and drainage system
Water Pump Set, Gas Water Pump, Diesel Engine Water Pump Set, Irrigation Water Pump
Weifang Huayuan Diesel Engine Manufacture CO.,LTD , http://www.cnhypower.com