Headquartered in Frauenfeld, Switzerland, ThalmannMaschinenbau AG specializes in sheet metal bending. The company entered the market in 1960 and, following the first manual operation of the machine, continuously introduced hydraulic drive and hybrid machines for sheet metal cutting and bending. Now, the company has been able to offer a wide range of standard and special machine tools for forming sheet metal up to 18.2m, which can be bent up to 3mm thick sheet metal (400N/mm2).
Thalmann offers machines for both small and large industrial applications. “For example, industrial metalworking equipment uses our two-machine linkage bending machine to machine generator façades and ICE train dams. But a small metal processing company bought the same machine because they produce custom siding and need to use To the function of the two-machine linkage bending machine." explains ThalmannMaschinenbau global sales MarcoCappello.
Improving precision is not as simple as it seems at first glance: the two-machine linkage bending process for metal forming is used for the hemming and contouring of sheet metal. This is a relatively gentle process in which the curved beam rolls up around the fulcrum of the material without damaging the surface of the metal sheet. The bending machine is usually composed of a bottom beam on which a metal plate is placed. The top beam presses the metal plate on the bent side against the bottom beam, and the curved beam moves upward to finally bend the metal plate into a desired angle.
Thalmann's control shaft technology ensures high-precision bending. The precision of the two-machine linkage bending machine is up to ±0.5° (basic model is ±1°), and the bending angle is up to 143°. Due to the high-performance hydraulic device, it takes only three seconds to complete the first direction. Outer and rotating strokes. The ThalmannTC and TD models of the two-machine linkage bending machine are equipped with two curved beams; during the bending process, the metal plates can be bent up and down without rotation. This speeds up the bending process and significantly increases the capacity of the press brake. A total of nine axes need to be controlled in the two-machine linkage bending machine.
CX series embedded controllers perform complex CNC functions The automation of the Thalmann bending machine is carried out by Regatron AG from Rorschach, Switzerland, and halmann has been successfully cooperating with the company for 25 years. “The first control system we built (currently still in operation) is based on a hard PLC,†said Felix Lanter, manager of R&D at Regatron Control and Drive Technology. However, as early as 1991, Regatron adopted the first PC-based control system, which used MSDOS computers. Then, in 2003, they used the first industrial PC with Windows and Ethernet technology ( IPC). “In 2010, we turned to Beckhoff control technology,†continues FelixLanter. “The ever-increasing level of precision in modern machinery requires changes in control systems across generations. The most important reason we chose to use the Beckhoff solution is to consider that Beckhoff can provide a hydraulic software library. When driving three servo motor shafts and up to six other hydraulic axes The software library will show great advantages."
Regatron software programmer Patrick Ruf further elaborated on the advantages of Beckhoff technology. “The CX1020 embedded controller creates an economical, scalable and technically high quality control system. Suitable servo drives and analog bus terminals can be used to drive the axes. In addition, we have created control solutions. Great flexibility to choose from a wide range of signals. For example, the control solution can be extended when the customer-specific requirements have to be met. The software also has the flexibility; we use the Beckhoff automation software TwinCATNCPTP We can continue to easily use the existing Windows-based user interface. We can use TwinCATADS to modify the control system without major changes."
Integrated security technology
“Of course, an important aspect of the press brake control solution is operational safety,†explains StefanKern. To meet mechanical safety standards, Thalmann uses the Beckhoff EL6900 Safety PLC Terminal Module, which is seamlessly integrated into the EtherCAT Terminal System. The TwinSAFE solution is SIL3 certified and complies with IEC61508 and DINENISO13849PLe standards. Security functions such as emergency stop, security door monitoring, and two-hand control can be easily selected and combined. They can be easily configured in the standard TwinCAT System Manager and run as device programs on the same PC platform. Security functions can be connected to device programs but are independent of each other.
Upgrade according to priorities
For equipment manufacturer Thalmann, they always put customer needs first. As a result, they offer not the traditional standard equipment, but custom equipment that takes into account customer needs, which vary in size, length and functionality. “The range of customer needs allows us to use components, systems and control systems that can be modified,†explains MarcoCappello. StefanKern's design director also holds the same view: "The complexity of equipment and control systems must be optimally matched to each other. Currently, we are working on a project that, due to cost, must save some functionality. This allows us to use The basic model is equipped with a smaller range and more targeted functions."
This concept is important for control solutions, which must reflect the needs of the device in programming. “On the other hand, we want to keep the design as uniform as possible,†explains software expert Patrick Ruf. “We designed the control solution architecture to take into account the fact that we can easily extend the scope of any feature. We also tried to make all devices compatible with each other so that even the oldest machine can Update and upgrade."
EtherCAT servo drive: dynamic performance is under control
The servo motor driven bending machine shaft is controlled by Beckhoff's AX5000 series EtherCAT drive. In terms of servo motors, Thalmann uses the Beckhoff AM3000 series of wound-pole motors. The hydraulic valve is controlled by the EtherCAT analog output terminal module EL4001. The position and angular position of the axis are measured using the digital absolute value rotary encoder terminal module EL5001. Device programming also includes a number of monitoring functions that ensure trouble-free operation. For hydraulic oils, for example, whose temperature is monitored, the flow rate is measured and the oil filter is checked. "One of the big advantages of the Beckhoff Bus Terminals is that we can use them to control almost everything," FelixLanter said.
Remote maintenance and diagnostics - new possibilities
ThalmannAG's bending machines are sold all over the world. In this regard, the potential service options for PC-controlled devices have become interesting. “When Thalmann is still in the past to provide traditional services, web-based remote services, especially for two-machine linkage bending machines, are a very interesting alternative.â€
(Finish)10-12 Ton Electric Pallet Truck
Zowell Electric heavy duty and durable pallet truck has great advantages in the glass and mold manufacturing industry.
We can customize the pallet truck as per your detailed requirements on fork length, fork width, lifting height and even fork height.
Not like Mini pallet truck, it is strong enough to load heavy duty goods.
The lithium battery pallet jack is also optional.
1. Electronic
control system
The electronic control system used by this truck is sensitive, ensuring a high
reliability. There are optional controller selections, including Cutris, ZAPI
or standard controller system.
2.
Regenerative braking
The regenerative braking control system can transform and store the kinetic
energy during braking, thus saving energy. This also increases the endurance
mileage, reduces brake pad wear and reduces the failure rate and usage costs.
3.
Multifunctional handle from FREI, Germany
The multifunctional handle is imported from Germany. The operators can control
the moving speed easily through the use of the handle, which is equipped with
an emergency reverse button. This effectively protects the operator against
injury in the event of an accident. The handle can achieve braking in both
vertical and horizontal positions, thus improving the tugger safety.
4. Emergency
reversing button on the handle
This truck can carry out emergency reversing. During the backward movement,
once the back of the operator touches something, the operator will naturally
hit the reverse button on the handle with their body. The truck will then
immediately reverse, thus protecting the operator against injury.
5. Emergency
power-off switch
The power can be rapidly cut off in an emergency to ensure safety.
6. Electric power steering system (EPS)
Compared with the traditional mechanical steering, EPS helps the driver with turning by using an electronic control device to produce auxiliary power at a relative level and direction according to the torque signal and speed signal. This makes operation by the driver more convenient and precise, so that movement is stable and reliable.
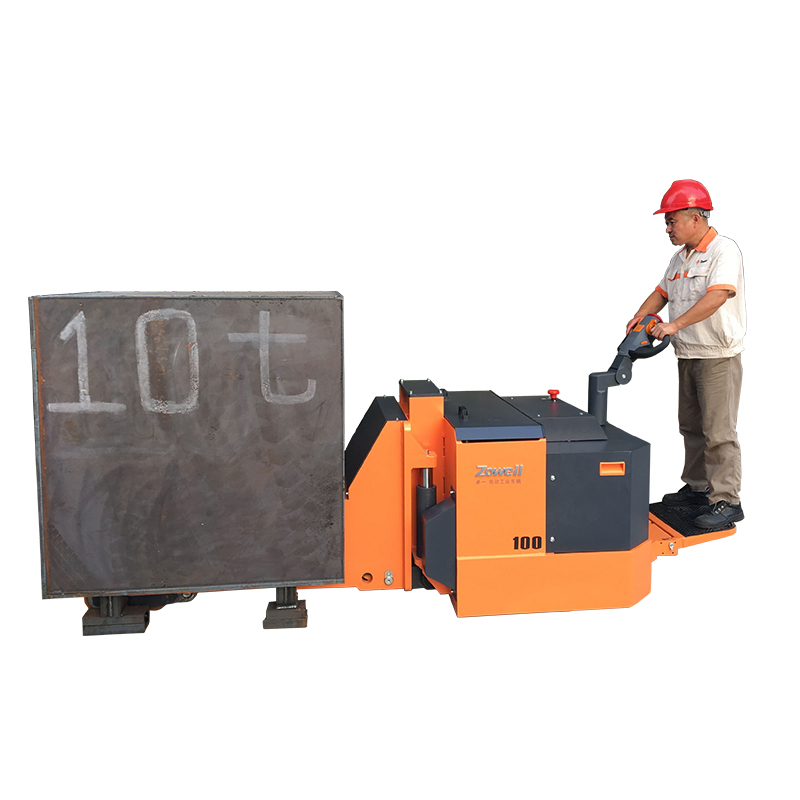
Full electric pallet truck,electric pallet jack heavy duty,Raymond pallet truck,Hyster pallet trucks
Suzhou Pioneer Material Handling Equipment & Technology Co., Ltd , https://www.zowellforklift.com