Project Description ◠Project Background The 1× and 2# units of the 2×300MW coal-fired power plant project in Central Java, Indonesia are EPC projects undertaken by China Chengda Engineering Co., Ltd. The project contract amounted to USD 510 million, which is the largest in China so far in Indonesia. The project was delivered to operation in October 2006.
SIS (Supervisory Information System in Plant Level, plant level monitoring information system) is a set of real-time plant-level monitoring information system between the DCS of the coal-fired power plant decentralized control system and the related auxiliary program control system and the plant-wide management information system MIS. It is an important part of the digital power plant. . The SIS system can provide real-time and reliable production real-time and historical data for the power plant business management decision-making level, and provide scientific and accurate production economic indicators for the power generation enterprises under market operation. The SIS system mainly processes real-time data, completes monitoring and management of production processes, fault diagnosis and analysis, performance calculation, analysis, and production scheduling. Many of the data managed by SIS are important basic data related to power plant production costs and quote information. From a management point of view, SIS first provides real and important on-site real-time data for the safety and stability of power plants, control of corporate costs, and increase the productivity of enterprises, while at the same time it can efficiently and accurately preserve a large amount of precious historical data produced by enterprises. . With advanced, scientific and effective data mining tools, accurate and professional calculation and analysis models, historical data saved and managed by SIS will become valuable resources for enterprise safety and economic operation.
â— System Configuration Each unit DCS system and auxiliary system are connected to Hessman's switch RS2-TX through an interface computer. OPC Server is installed in the interface computer as the interface between the control layer and the SIS layer data collection. The DCS OPC Server is provided by the DCS manufacturer. The OPC Server for the auxiliary system is provided free by us.
The interface computer, database server, and application engineer station are all connected to the RS2-TX with exclusive 100M channels.
In order to ensure the security of the SIS system, a firewall is specially designed between the SIS switch and the administrative office building MIS layer.
Network topology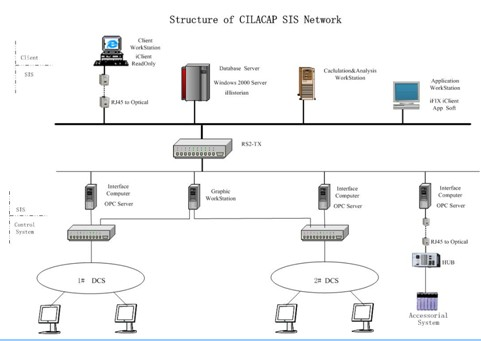
System Function The SIS system collects process control system data from various production sites, including: #1 Distributed Control System (DCS) network, #2 Distributed Control System (DCS) network, and auxiliary system network. The SIS system carries out unified monitoring and query of various production processes, and comprehensively processes the production data to form a plant-wide production report. At the same time, the entire plant real-time and historical database is established to meet the requirements of MIS and related management departments to query and process on-site process data quickly and efficiently. At the same time, SIS will complete plant-level performance calculations and provide a basis for cost calculation of power generation in the commercialization of power plants.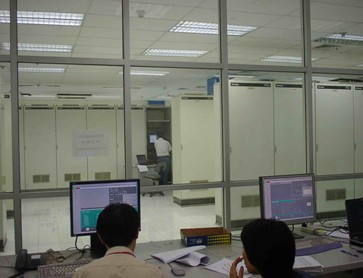
The system mainly implements the following functions:
â— Whole plant production process monitoring and management â— Real-time processing of production site related information â— Plant-level performance calculation and analysis functions System features SIS system uses advanced field control technology and computer network technology to achieve network redundancy and switch redundancy from the network. I, server redundancy, history database software redundancy and other functions, and ensure the technical feasibility, reliability, advancement, scalability of network centralized control system solutions from hardware and software selection, function design, network design and other aspects. The stability provides a reliable source of data for the stable and reliable operation of the entire system.
The specific features of the entire SIS system program are:
â— Professional-level network redundancy technology â— Secure and reliable network communication technology â— Professional and fast communication interface â— Convenient universal data upload interface â— Professional-grade industrial switch â— Reliable server redundancy technology â— Outstanding enterprise-class industrial real-time database â— Advanced monitoring software configuration technology â— Advanced database redundancy technology â— Easy-to-use and powerful application interface â— Complete SIS calculation function module â— Powerful historical data analysis system â— Practical production report module System integration product â— Network System: Hirschmann Switch â— Hardware:
1. Server: IBM ServerX335
2. Numerical calculation: IBMServerX305
3. Interface machine: IBMS50
4.HMI: IBMX50
5. Firewall: CISCOPIX-515E
6. Printer: Epson C7000
â— Software:
1. History database management software ProficyHistorian3.0
2. Interface Development Software ProficyiFix3.5
3. Antivirus software Norton10 user network version
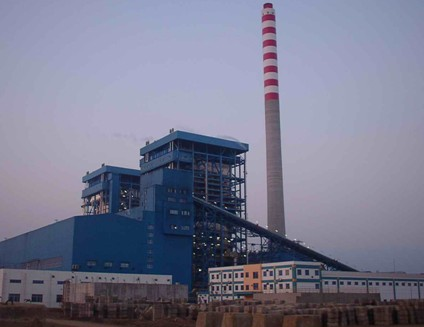
â— System Configuration Each unit DCS system and auxiliary system are connected to Hessman's switch RS2-TX through an interface computer. OPC Server is installed in the interface computer as the interface between the control layer and the SIS layer data collection. The DCS OPC Server is provided by the DCS manufacturer. The OPC Server for the auxiliary system is provided free by us.
The interface computer, database server, and application engineer station are all connected to the RS2-TX with exclusive 100M channels.
In order to ensure the security of the SIS system, a firewall is specially designed between the SIS switch and the administrative office building MIS layer.
Network topology
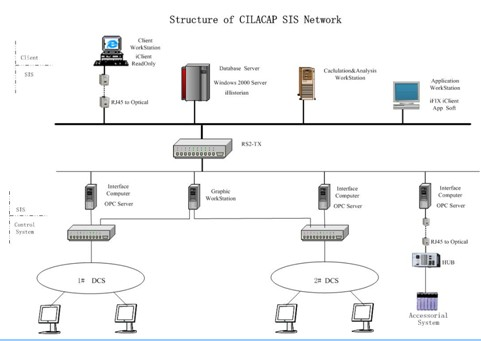
System Function The SIS system collects process control system data from various production sites, including: #1 Distributed Control System (DCS) network, #2 Distributed Control System (DCS) network, and auxiliary system network. The SIS system carries out unified monitoring and query of various production processes, and comprehensively processes the production data to form a plant-wide production report. At the same time, the entire plant real-time and historical database is established to meet the requirements of MIS and related management departments to query and process on-site process data quickly and efficiently. At the same time, SIS will complete plant-level performance calculations and provide a basis for cost calculation of power generation in the commercialization of power plants.
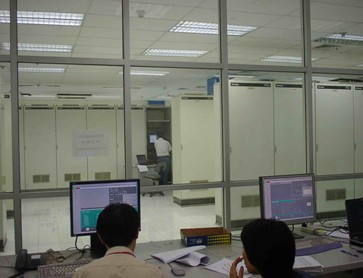
The system mainly implements the following functions:
â— Whole plant production process monitoring and management â— Real-time processing of production site related information â— Plant-level performance calculation and analysis functions System features SIS system uses advanced field control technology and computer network technology to achieve network redundancy and switch redundancy from the network. I, server redundancy, history database software redundancy and other functions, and ensure the technical feasibility, reliability, advancement, scalability of network centralized control system solutions from hardware and software selection, function design, network design and other aspects. The stability provides a reliable source of data for the stable and reliable operation of the entire system.
The specific features of the entire SIS system program are:
â— Professional-level network redundancy technology â— Secure and reliable network communication technology â— Professional and fast communication interface â— Convenient universal data upload interface â— Professional-grade industrial switch â— Reliable server redundancy technology â— Outstanding enterprise-class industrial real-time database â— Advanced monitoring software configuration technology â— Advanced database redundancy technology â— Easy-to-use and powerful application interface â— Complete SIS calculation function module â— Powerful historical data analysis system â— Practical production report module System integration product â— Network System: Hirschmann Switch â— Hardware:
1. Server: IBM ServerX335
2. Numerical calculation: IBMServerX305
3. Interface machine: IBMS50
4.HMI: IBMX50
5. Firewall: CISCOPIX-515E
6. Printer: Epson C7000
â— Software:
1. History database management software ProficyHistorian3.0
2. Interface Development Software ProficyiFix3.5
3. Antivirus software Norton10 user network version
Modular grinding sanding polishing abrasive station
For Modular grinding station, because its space limited, it decides that only size in specific range can be processed in this grinding table. Based on different uses of this machine, we can call the table different names, modular grinding station, Modular sanding station , Modular polishing station, Modular abrasive station, modular deburring station, modular harmonizing lines station, modular cleaning station.
Modular grinding station, Modular sanding station,Modular polishing station,Modular abrasive station
DARU Technology (Suzhou) Co., Ltd. , https://www.szdaruactivecontactflange.com